It’s been some time since I’ve provided an update, but fear not I have been busy behind the scenes.
First up I took my 3rd year BHI exams in May 2014, which also included the Drawing Clock/Watch Escapement exam that I had postponed from the 2nd year. The reason for the postponement was that I wasn’t confident that I could do my best unless I put in more effort than I was going to be physically capable of putting in. In the end I spent a good 2 months of my spare time doing nothing but teaching myself how to do a technical drawing and learn how to use AutoCAD. YouTube has some great videos to teach you how to use AutoCAD and the BHI’s booklet on drawing clock/watch escapements is a fantastic step by step guide on how to pass the exam.
I think if you follow the guide enough times; I did each of the examples at least 6 times, then it will be pretty hard to fail the exam, as you’re even allowed to take the booklet telling you how to do it into the exam.
The result, well, it proved my point and made me pleased that I had postponed the exam as I got the prize for the best drawing, as well as the best results for the Diploma in Clock and Watch Servicing!
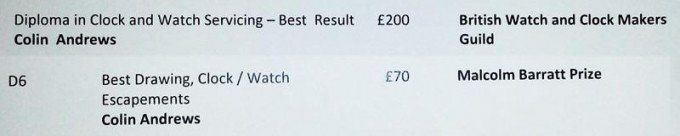
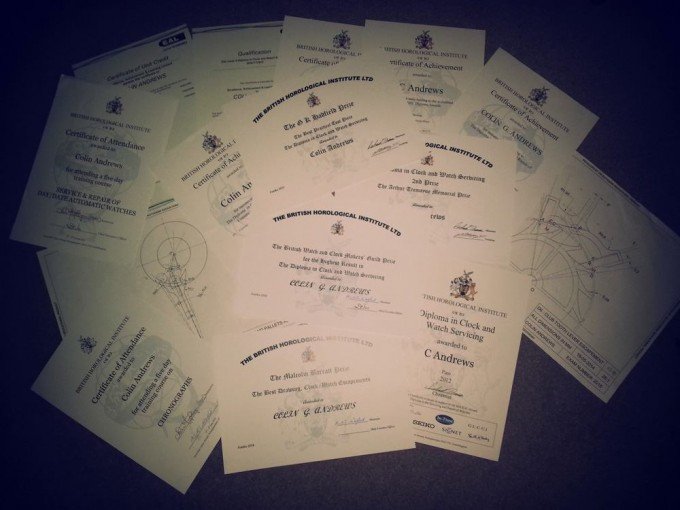
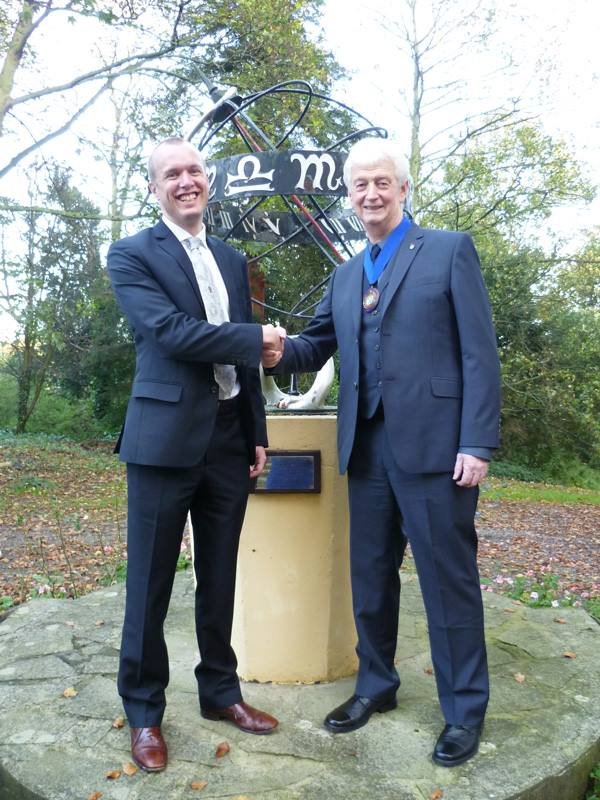
I had just one exam left to take before completing my MBHI, which was the advanced theory, although I aimed to go the full hog and take the additional exams get my FBHI title. In the end I again didn’t feel that I had enough time to complete the demanding portfolio of restoration (which involves making various parts, performing complex repairs as well as doing academic research for 5 watches), in the time available. So I just took the advanced theory exam in May 2015, and completed as much of the portfolio as I could, to hopefully finish in 2016.
It was a really difficult time to study for the advanced theory, as it felt like I was knocking my head against a wall with some of the topics. The booklets are, by the BHI’s own admission, old and outdated, and they proved to be almost impenetrable at times; with the feeling that you could only understand the topic if you already had some prior knowledge of it. But in the end I buckled down before the exam and passed. Surprisingly bagging myself another award in the process! This means I am now an accredited member of the BHI, which allows me to add the suffix MBHI to my name.

Working as a full-time watchmaker, I am always keen to improve my skills and learn new techniques. One of the things that I’ve started to really enjoy is polishing cases and bracelets, a service I provide to each customer. It’s really satisfying to turn something old and worn looking into something that looks brand new again. Often as a watchmaker the work you do is unseen by the customer, and so by refurbishing the outside visible parts of their watch, they are able to understand the care and attention you have taken with their timepiece.
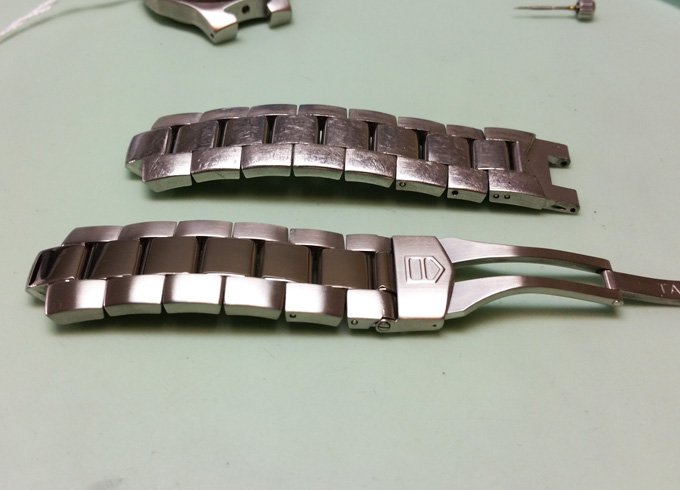
I was also kindly invited to the official handover ceremony for English watchmaker Robert Loomes’ new Everest Watch. As a celebration of 200 years of service in the British Army, the Gurkhas of Nepal were going to climb mount Everest. In a mirror of the original conquest of the peak by Sir Edmund Hillary and Tenzing Norgay who carried the British made Smiths watch to the summit, Robert had been commissioned to provide a modern day British watch to make the journey; with some of the pieces due to be auctioned off to raise money for charity. Sadly due to the earthquake in Nepal in 2015, the climb did not take place, but hopefully there will be opportunity to make the journey at a later date. (Please see the Jan 2016 for an update).
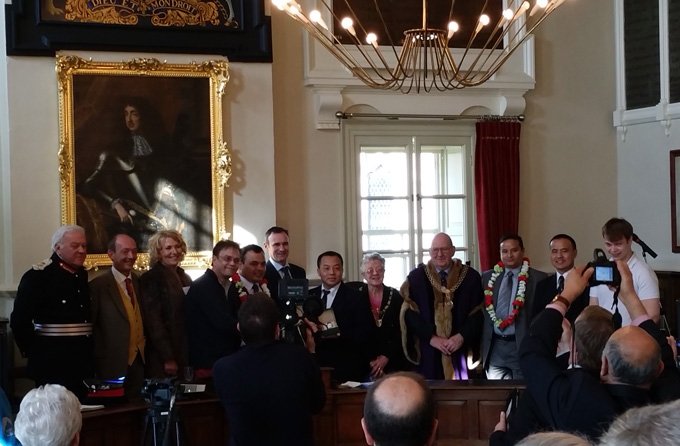
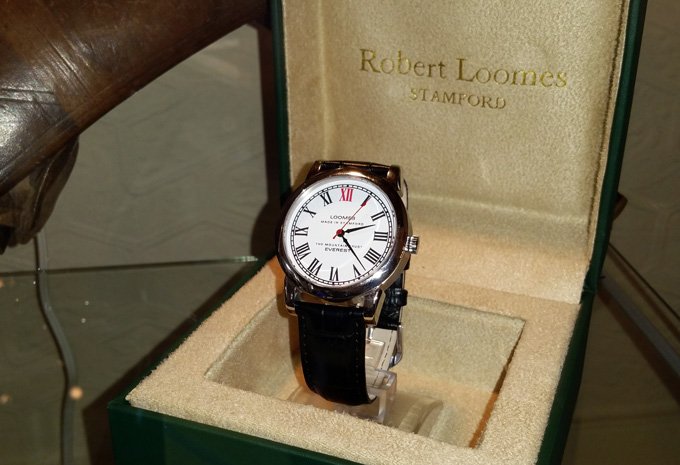
I’ve also been keeping myself busy with other, non-watch related activities. Along with doing Latin dancing a few times a week, I have thrown myself in at the deep end and volunteered for a charity boxing event for September 2015. I’ve never done anything remotely like this, and so along with pushing myself far out of my comfort zone, I am also raising money for Cancer Research UK.
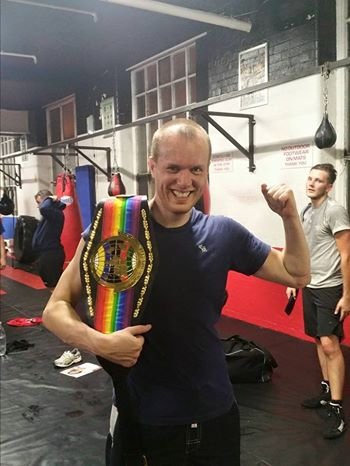
Update Sep 2015:
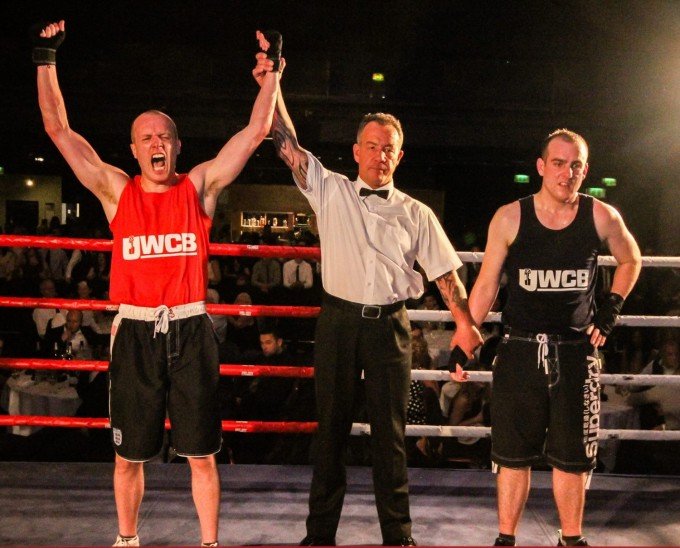
Update Jan 2016:
Robert Loomes has been in contact with regard to the expedition to climb Mount Everest in 2015. Although the climb did not reach the peak due to the conditions following the earthquake, they did however partially complete the climb and were able to put the watches through their paces. Robert writes:
“Whilst they did not summit, the team spend seventy days climbing in the Himalayas wearing our watches with temps down to -35 and to an altitude of 21,000ft. As Capt Dick Gale said when he returned them to the BHI (knowing the Smiths / Rolex history of the 1953 Hilary/Hunt expedition) “We carried your watches on Everest; they worked perfectly”
Andrew Cable
26 November, 2015 at 8:31 pm
I appreciate this probably isn’t the most appropriate post to ask this question but generally, do you recommend a certain lathe to start out with and where is the best place to search for them?
Colin
28 November, 2015 at 12:32 pm
Hi Andrew,
I use a Sincere brand of lathe. It’s a Chinese brand. I brought it brand new from eBay. It’s difficult to find a decent lathe though on eBay that’s 2nd hand, as you won’t be able to test it.
Search for “mini lathes” or “micro lathes”. You will want one that you can get add-ons for, particularly collets, 3 jaw chuck and a cross slide; and be sure to check that it come with a motor too.
Shaun Caldwell
13 December, 2015 at 3:38 pm
Wow Colin, well done! Congratulations on the MBHI.
You’re achievements since you made that career change have been remarkable. I stumbled across your website when researching about making a career in watchmaking.
I’m a physics teacher from the UK currently teaching at a college in China but looking to make a career change. I initially came across watchmaking earlier in the summer when I was flying back home – I read an article about watchmaking in the FT and how they’re was a shortage back home.
And ever since I got back to my current job, I seem more motivated to make the switch and get stuck into it. To me watchmaking has the application of physics and engineering but also the creativity of art and a fine painting. It seems like real trade where I can learn and apply the things I’ve learnt to something physical, and I think that’s something that I’m looking for. That I would find rewarding.
Also, I find it massively coincidental that I am currently in China, lived here for 5 years, learnt Mandarin to a good standard but not mastered and participated in two white collar boxing events for charity – well done on raising all that money and retiring undefeated, it looked like a fantastic night!
Well anyway, I’m considering all my options from different WOSTEP schools and the BHI route – thanks for the detailed insights into each one. After some more research which I’m sure will include reading the other articles you’ve posted about your experiences on here and some further enquiries, I’ll make a decision.
Keep up the good work.
Best wishes,
Shaun
Colin
20 January, 2016 at 8:08 pm
Thank you for your message Shaun. Watchmaking is a great career choice, and you’ll find the skills you’ve picked up in China; particularly patience, will go a long way. Let me know what route you go down or if I can help at all. Colin
Roland
5 February, 2016 at 7:02 pm
Hello Colin;
Keep coming back to read your interesting webpage 🙂
I red your brief note about polishing cases and bracelets; which I plan to do with my bi-metal Rolex Submariner. I’ve seen some good YouTube video’s about buffing & polishing, but hardly any of them go in great detail about which compound, grit sizes and what not to do. Interesting to learn was the difference between buffing and polishing. Not to round edges of the watch case.
But how does one bracelets, like the one you are showing? What tools and grits are used (paste or sanding paper/linen?). Sequence of buffing/polishing?
Could you write a little (or an article) about that?
Hope to hear…….
Best regards: Roland, Denmark.
Colin
22 February, 2016 at 12:06 pm
Hey Roland,
Thanks for your message!
I have taken a lot of photographs of the polishing process, and so hopefully I can put a full article together soon. In the meantime I can explain the basics of the process:
– All case/bracelet polishing is done on a lathe (unless mentioned otherwise).
– There are special polishing compounds that look like bars of soap and come in different colours depending on their grit size. I’ve experimented a lot with the different types and found what works for me; although most people have their own preferences and get similar results. I use a brand called Dialux. I use green and blue for steel, and red for gold. For high mirror finishes on steel I may also use a super fine compound like black or white with a special mop made from similar material to a parachute.
– The polishing compounds are used with mops. A felt mop is for removing scratches and a cotton mop is used for buffing. You can use the same compound on different mops and the effect will change. The amount of pressure you use on the mop has a huge effect too.
– Never cross contaminate mops i.e. never polish with green then go straight to blue without cleaning the previous compound off. You want each mop to be as pure as possible. I store each mop in a bag after use to stop it getting contaminated.
– For removing heavy steel scratches I used a grit wheel; the brand is Artiflex. This is a rubber like wheel that you do not use with a compound. It can even out all the marks, but will leave a light brushed finish, so it’s not very good if you later want a high polish finish.
– For a brushed finish I used either a Alluminium Oxide Bufflex wheel, or a wheel I’ve made out of Garryflex.
– When polishing gold, less is always more. Gold is so soft that you will remove a lot of material fast if you are not careful. I just use the red compound, which is Iron Oxide, on a cotton mop, and go over each area for a few seconds. I will never polish the edge of a caseback or inside edge of a case; as you can very easily change the shape and so the watch case will not fit together as well any longer. To get a brushed finish on gold I will use Garryflex and do it by hand.
– For when you have a two-tone or two-finish then you will want to start with the polished and softest areas first. So if you have gold and steel, you will start with the gold, if you have a brushed and polished finish you will start on the polished part. Once that part is finished you then tape over the finshed area so that you can work on the other area without damaging your previous work.
There’s a lot more I could mention, but hopefully that’s a good overview!
Roland
22 February, 2016 at 12:29 pm
Thank you very much for this very elaborated explanation ! Excellent indeed!! I have to, and will read this article a few times to let in sink in. My bracelet is still soaking in a soap solution, awaiting a cheap ultra-sonic cleaner. This cleaner was also meant to remove the paste between the differnet polishing phases. I will wait till your article comes up, as I want to make sure I do it right. Meanwhile I found a nice NATO-strap, with “gold” buckles, and it compliments the Bi-color Submariner actually very good, so I’m not in a hurry 🙂
I’ll keep a close eye on your webpage…..
Thank you very much for you time and effort 😉
Friendly greetings from Denmark;
Roland